Looking for a fun DIY project to start building your skills? Try out making this DIY picnic table for squirrels. You...
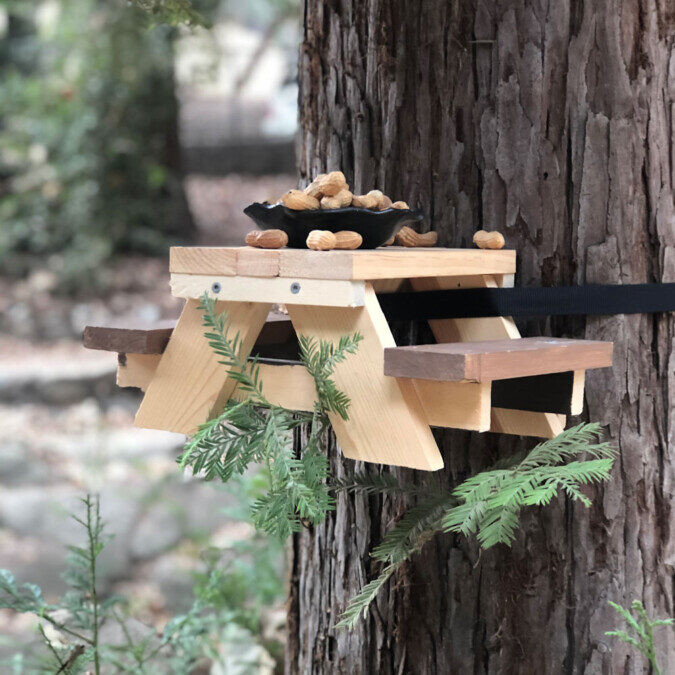
Looking for a fun DIY project to start building your skills? Try out making this DIY picnic table for squirrels. You...
While I was redoing my tiny 5’x6’ home office set up, I wanted to incorporate a white board, but do it in a way that...
This post was sponsored by Surebonder. All opinions are my own. When I moved into my apartment almost 6 years...
If you've been following along, you know that I've taken on my biggest DIY project to date: building a Murphy bed for...
The 200 ft2 rental studio apartment I'm working on needed a Murphy bed so I built one with an industrial inspired...
For highlights of this project, watch the video! In case you haven’t been following along, here’s a recap of the...
Did you read my first post in this "how to build a Murphy bed" series? In case you missed it, here's a recap. I’ve...
If you’ve been reading my newsletter and following me on Instagram, you know that I’ve undertaken a new big/small...
I love it when people share the projects they've made that are inspired by watching my videos or reading my blog. It's...
I recently built a new headboard for my bedroom and needed a new bedside table to go with it. I didn't want to spend a...
When I moved into my LA apartment, I had bought a bed frame that didn't have a headboard - the plan was to build...
I built this outdoor chair right on the dining room table of my small apartment, using just a few hand tools - if I...